Constructing a Tanpura
It is a well-known fact that generally, the best sounding tanpuras in India come from a place called Miraj in Maharashtra. The following pages will deal with the process of constructing a tanpura according to those built in Miraj. The basic process may differ slightly in Calcutta, Delhi or other manufacturing towns, but the outline will be the same. The tanpuras of Southern India, which are built mainly in Thanjavur are, except for their shape, very different to their Northern counterparts.
Of the two types of wood used for building tanpuras, tun (red cedar) is better and more commonly preferred to teak. This is due to the fact that although the quality is very similar, tun is slightly lighter and less dense than teak allowing a better resonance. However, teak tanpuras have a very good name and are often praised for their beautiful sound.
The wood must be well seasoned for a few years or at least kiln-dried to be able to keep its shape and to withstand seasonal changes in climate. It is extremely important to use a piece of wood without embellishments such as knots. Unfortunately due to the ever increasing difficulty of obtaining good quality wood, it is not always possible to live up to these ideals. It is often a dilemma for the manufacturer when due to the pressure of time, the delivery of the instrument cannot be met without having to make unwanted compromises with quality. It is not uncommon, for example, to see the soundboard being made from two pieces of wood.
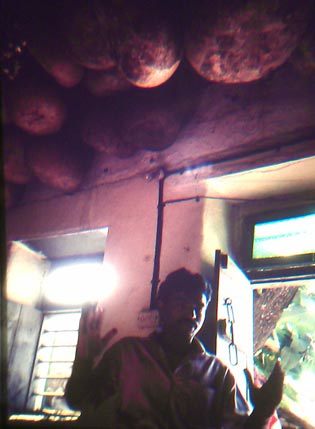
After the wood has been carefully chosen, the different components are then cut to size and carved ready for construction. There are 5 main parts to the instrument, not including leaves, pegs bridges etc. They are;
- The soundboard or tabli
- The resonating bowl or tumba
- The neck or dandi
- The fingerboard or patta
- The neck heel or gullu